Craft the Ideal Underfloor Heating Pipe Layout
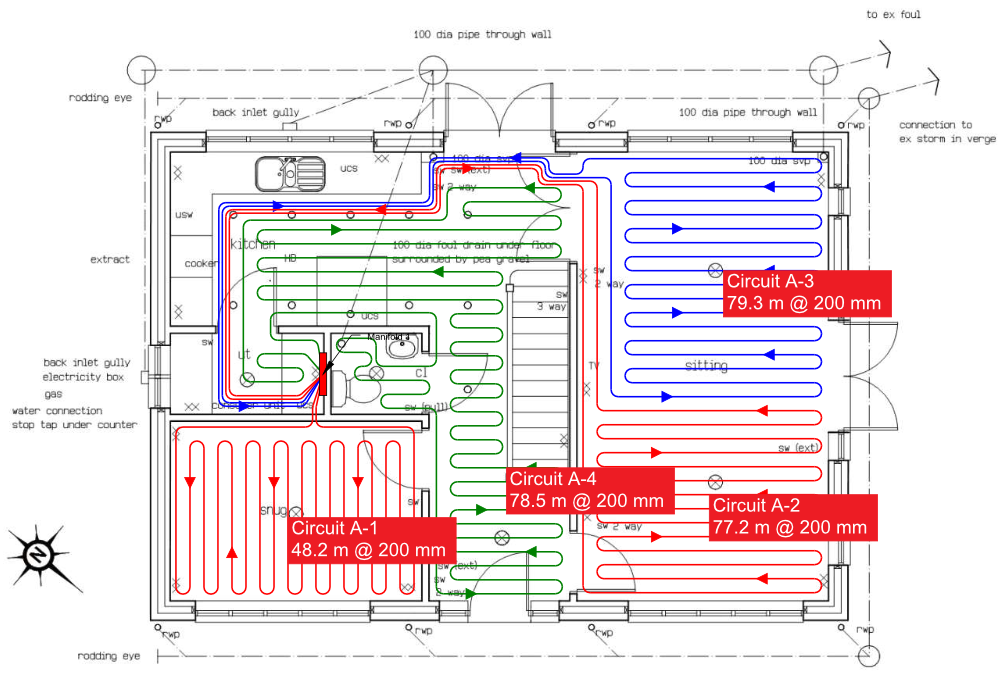
Underfloor heating pipe should be laid at 200mm centres dependent upon design.
The maximum heat output for underfloor heating systems is 100 W/m2 for concrete floors and 70 W/m2 for timber suspended floors. For any underfloor heating system to work efficiently, the property needs to be built to current building regulations and no rooms should lose more than the above output.
Condensing boilers are very efficient with underfloor heating. When using combination boilers you must check with the manufacturer that the boiler can be fitted with a secondary pump.
Underfloor heating systems can be combined with conventional radiator systems but the underfloor heating system needs to be on a completely separate system, i.e. the flow and return for the underfloor heating needs to go all the way back to the boiler, normal control is by 2 port valves, like a normal S-Plan system.
Advice on Insulation and Floor Constructions
We recommend a minimum of 50mm of Polyurethane insulation for the underfloor heating system. This is very high quality insulation and can be used for both concrete and timber suspended floor constructions. All insulation requirements should comply with current building regulations. See our floor construction page for more information.
We do not supply insulation. Any builder’s merchant will stock insulation such as Xtratherm or Kingspan. The quote is based on clipping the pipe direct to the insulation board. We supply the pipe clips. Use a minimum of 65mm of screed on top of the insulation for concrete floors, for timber suspended floors see the floor Construction page. Plastic sheets must not be laid on top of the pipes.
Also 50 mm liquid screed or fibre screed can be used for screeded floors. It is important to use a plastic membrane on top of the insulation for liquid screed. Edging strip must also be used all around the perimeter of the walls.
Moisture Content in Screed and Floorboards
The screed must be allowed to dry for a minimum of 4 to 6 weeks before the heating is operated. As the system is used for the first time, the mixing valve must be set to minimum setting to let the moisture in the screed dry out. The temperature should be increased by two degrees every day until the mixing valve is set at 45°C.
Care must be taken to protect the pipework whilst installing the screed. Finally the floor finish is laid. Underfloor heating works well with almost any floor finish; tiles, carpets (use carpets with a resistance of less than 0.15 m2K/W), timber floors, plastic etc. The floor coverings and the adhesive must be suitable for the temperatures that underfloor heating will provide; the maximum temperature they need to resist being 40°C. Carpet and underlay together must not exceed a thermal resistance of 2.5 Tog.
Floorboards must have a moisture content lower than 7% before they are installed. We do not recommend floorboards thicker than 25mm, see our Floor Construction page for more information about floorboards. Always check with the manufacturers of any floor finish that it is suitable for underfloor heating.
Heating in Toilets and Bathrooms
As these areas are usually very small, extra heat might be needed. Therefore, it is standard practice to install towel rails combined with the underfloor heating.
Isolating Valves Before Mixing Valve(s)
We strongly recommend that the plumber installs ball valves on the flow & return feeding the ufh system, in case the pump and mixing valve should need servicing in the future.
Please Note
Always check with the manufacturer of the floor covering if it can be used for underfloor heating. Timber floors need to have a moisture content below 10% to avoid shrinkage. The system must be operated for 21 days with a very low temperature to dry the screed, then the floor covering can be laid. Also note that the screed must be allowed to dry for 6 weeks before the underfloor heating is operated.